|
Time Travel Research
Center © 2005 Cetin BAL - GSM:+90 05366063183
- Turkey/Denizli
Propulsion: Nuclear vs. Chemical
A Technical Process Description
David Kozdron
Jeff Tieman
Submitted: November 24, 1999
Sophomore Engineering Clinic I
Propulsion Systems
The purpose of this project is to provide background information on 2
types of propulsion systems for the NASA Mars mission, among other things. This
report will have the goal of determining which form of propulsion to use (nuclear
or chemical). The benefits and disadvantages of chemical propulsion will be
weighed against the benefits and disadvantages of nuclear propulsion. Areas of
discussion will include thrust, weight, fuel, cost, environmental factor, and
degree of safety.
Introduction to Chemical Propulsion
Chemical Propulsion is an extremely broad topic, as there are hundreds
of elements and compounds that can be used as fuel. Each of these propellants
have their own properties, such as the temperature that they burn at and how
much thrust they produce. Chemical propulsion systems have been the mainstay in
the world's space programs thus far. Due to the large amount of propellant that
these systems require, many new technologies have been proposed and are
currently being tested. A nuclear thermal rocket engine uses approximately 50
percent less mass of propellant than the theoretically best chemical engine [this
upper boundary (based on thrust produced / efficiency) is near a limit with the
Space Shuttle main engine].
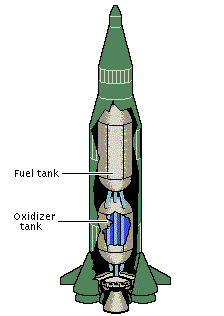
Figure 1: Location of the fuel and oxidizer tanks[4]
A chemical rocket is self-contained, which means that it carries both
fuel and oxidizer internally, rather than obtaining oxidizer from the outside
atmosphere as a jet engine does. Because of this, it can be used for propulsion
outside of the atmosphere [4].
How does it work?
General:
Thrust to propel a rocket is based on Newton's Third Law of Motion,
which states that for every action, there is an equal and opposite reaction.
Inside the combustion chamber, the fuel and oxidizer are mixed and burned. In
the case of the Space Shuttle, the main engines burn hydrogen and oxygen from
the external tank. The resulting expansion of burning gases creates pressure
inside the chamber. All forces inside the chamber other than directly up and
down are equalized by their opposite and equal force, preventing the rocket from
moving left or right. The upward thrust created by the burning gases cannot be
equalized because of the open nozzle at the end of the rocket. This forces the
rocket upward. The amount of thrust produced by the rocket engine depends on the
mass and velocity of the burning gases when they leave the combustion chamber
[4]. The combustion chamber has a converging section to the narrowest portion,
which is called the throat. At this point, the passage begins to grow wider. The
nozzle diameter can be four or five times that of the combustion chamber. In
liquid-propelled rockets, regenerative cooling is often used to help in heat
transfer at the throat, since this is where the greatest amount of heat is
generated [1].
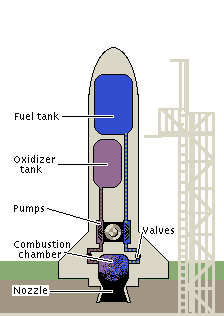
Figure 2: Parts of a Chemical Propulsion System [4]
Basic Types of Chemical Propulsion Systems
Solid-Propellant Rockets:
Solid-propellant rockets consist of the payload (if there is one), and
the rocket engine. The propellant charge is stored and burned in the motor [4].
Liquid-Propellant Rockets:
Liquid-propellant rockets contain two main tanks, one containing the
fuel, and the other holding the oxidizing agent. In a small liquid-propelled
rocket, the fuel and the oxidizer can be pressurized and forced into the rocket
engine with an inert gas. However, in larger rockets, this process would make
the tanks too heavy. Therefore, between the tanks and the rocket engine are
pumps that produce the required delivery pressure. The pumps required are driven
by a gas turbine and are high-capacity to manage the large amount of propellant
used [4].
Hybrids:
In a hybrid rocket the fuel is solid, and the oxidizer is liquid. The
liquid is carried in a pressurized container above the fuel, which burns outward
from a center hole. This system combines the advantages of solid propellant and
liquid oxidizer. The solid is easier to handle and the liquid allows for the
regulation of the rate of burning [4].
Propellants
Early solid-propellant rockets used a mixture of 60 percent saltpeter,
15 percent sulfur, and 25 percent charcoal for combustion. These are the same
ingredients that are used in black gunpowder, but in different proportions,
which allows the rocket propellant to burn slower. In November 1918, Robert
Goddard improved the design by using smokeless powder instead of black powder.
Modern solid propellants are synthetic rubbers with an oxidizer mixed in during
manufacturing [1]. They are good fuels, and can be handled more safely. The
addition of powdered metals such as aluminum can make this synthetic rubber fuel
more powerful [2].
Liquid-propelled rockets originally used gasoline as fuel, then more
recently used ethyl alcohol and kerosene. Burning ethyl alcohol with liquid
oxygen was a problem because the low boiling point of alcohol creates
considerable evaporation losses. From this, hypergols were discovered. A
hypergolic propellant ignites spontaneously when the fuel and oxidizer are
brought together, eliminating the need for an ignition source. The most
efficient fuel is liquid hydrogen, which is used for the US Space Shuttle. This
fuel source, however, is rather difficult and dangerous to handle due to its
high flammability [4].
Statistics vary for different propellants and rocket engine systems. The
amount of thrust produced primarily depends on the mass and velocity of the
burning gases.
The Space Shuttle
The shuttle is a manned space plane, capable of performing various
missions with a payload of about 30,000kg (65,000 lb). It can carry up to 7 crew
members. The orbiter stage was designed with a theoretical lifetime of 100
missions. The orbiter was launched into orbit with the help of two solid rocket
boosters and an external tank that fall away back to earth after use. The two
solid rocket boosters are the largest solid-propellant rockets ever built in the
United States [4].
The following is an excerpt from [3]:
"The two solid rocket boosters are each 149.1 feet (45.4 meters) high
and 12.2 feet (3.7 meters) in diameter. Each weighs 1,300,000 pounds (589,670
kilograms) when on the launch pad. Their solid propellant consists of a mixture
of Aluminum powder, Ammonium Perchlorate powder, and a dash of Iron Oxide
catalyst, held together with a polymer binder. They produce about 3.1 million
pounds (13.8 million newtons) thrust each for the first few seconds after
ignition, before gradually declining for the remainder of a two-minute burn.
Together with the three main engines on the orbiter, this provides a total
thrust of over 7.3 million pounds (32.5 million newtons) at liftoff.
The external tank is actually three components in one: a liquid oxygen
tank located in the forward position; a liquid hydrogen tank located aft; and an
intertank assembly that connects the two propellant tanks and houses the forward
solid rocket booster attachment points. The external tank weighs approximately
1,655,600 pounds (751,000 kilograms) when filled with propellants and 66,000
pounds (29,900 kilograms) when empty.
The Space Shuttle main engine is the most advanced liquid-fueled rocket
engine ever built. Its main features are variable thrust, high performance,
reusability, total redundancy, and a fully integrated controller. The
performance of the engine is the highest thrust for its weight of any engine yet
developed. Fuel is supplied from the tank at a rate of about 178,000 liters
(47,000 gallons) per minute of hydrogen and 64,000 liters (17,000 gallons) per
minute of oxygen. The main engines use a staged combustion cycle in which all
propellants entering the engines are used to produce thrust more efficiently
than any rocket engine developed previously. In the staged combustion cycle,
propellants are burned partially at high pressure and relatively low temperature,
and then burned completely at high temperature and high pressure in the main
combustion chamber. The rapid mixing of the propellants under these conditions
is so complete that a combustion efficiency of about 99 percent is attainable."
Introduction to Nuclear Propulsion
Nuclear thermal propulsion is a broad topic to describe several new
engine designs that could begin to come available in the new millennium. The
most common are the NERVA (Nuclear Engine for Rocket Vehicle Application)
designs developed and tested in the 1960s. Primary focus of this section will be
given to the NRX series engine developed by this program. The reason is that
this was the most developed engine and to rebuild and develop a flight ready
engine is minimal in terms of cost and time. This section will describe the
history of the nuclear thermal propulsion engine, examine how it works and
comment on the current status. Nuclear electric propulsion will not be looked at
in detail because it is not as powerful, and thus not very useful in
interplanetary operations.
History of Nuclear Thermal Propulsion
In 1960, the NERVA program was begun to develop an engine for possible
use in the Apollo program. The program lasted 11 years and was terminated in
1971. During its lifetime, the NERVA program developed two separate engines. The
first was the NRX. This engine was rated at 1100 – 1500 MW of power output with
75,000 lbs of thrust. The other engine was the Phoebus engine. This was a much
more powerful engine rated at 4500 MW of power and 250,000 lbs of thrust.
Although both designs were tested, the NRX was further developed. By 1971, a
fully integrated engine complete with LH2 turbopumps, valves and
nozzles, was tested at simulated altitude. At the time the program was
terminated, focus had begun to shift to developing a fully flight operational
engine [5].
Nuclear Thermal Propulsion
Since nobody has fully developed a nuclear thermal engine, information
on design is subject to change. This section will describe the theory of
operation, as well as some of the potential designs for the future.
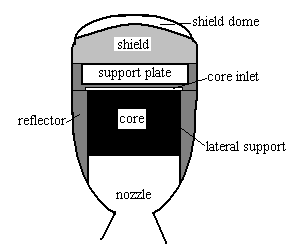
In nuclear thermal propulsion a nuclear reactor heats a coolant to
extremely high temperatures and expels it out a nozzle, similar to those used in
chemical propulsion. In nuclear thermal propulsion, the nuclear reactor takes
the place of chemical energy released in the combustion of LH2 and LO2
propellants. The reactor core consists of Uranium – Carbide fuel enclosed in a
graphite matrix. When active, the uranium atom is split, creating tremendous
amounts of energy.

Control drums surrounded by beryllium cylinders reflect or
absorb neutrons from the atoms. These control drums
surround the core and act as a shield. Liquid hydrogen fuel is
injected into the core and heated to a temperature of
2500 K by the nuclear reaction. Most of the hydrogen is then
ejected out of the nozzle to propel the engine
with a small amount diverted to run the turbopumps. The
turbopumps then pump more hydrogen fuel into the reactor core [6].
In any nuclear power device, shielding is of the utmost importance.
Shielding protects both the potential crew as well as delicate equipment on
board. Shielding is required because during a nuclear reaction, radioactive
material is created and high-energy gamma rays are emitted.
In the nuclear thermal engine, a ZrH shield located on top of the
reactor protects the turbopumps and crew from the core. Ejected propellant is
not of much concern because it does not become radioactive. The nuclear fuel
element (fuel for the nuclear reaction) from the core is also of little concern
because it is a small amount and will quickly disperse into space. However,
shielding from the burn is important, as the gamma rays emitted from the core
will destroy any life. This is accomplished by a combination of tungsten shield
and liquid hydrogen. The liquid hydrogen is the contingency tank, and is just
extra shielding. The entire tungsten shield will protect the crew during the
burn, then unfold to protect from the low intensity long-term radiation. When
this is complete, docking and extra-vehicular activity (EVA), or spacewalk, will
be permitted [5].
The most developed engines today are the NERVA engines. These engines,
developed in the 1960s and early 1970s, are a good indication as to what nuclear
propulsion can provide.
|
NRX |
Phoebus |
Power |
1500 MW |
4500 MW |
Thrust |
75,000 lbs |
250,000 lbs |
Isp |
825 s |
820 s |
mass |
15,000 lbs |
40,000 lbs |
Several ideas have been thought up to enhance the capabilities of the
nuclear thermal engine. One idea is to run the engine at low power after the
burn. This will allow for the generation of electrical energy during the
remainder of the trip. Another idea is to insert high temperature plumbing into
the core after the burn. The energy gathered by this plumbing could then
generate enough electricity to run an electrical engine. This will allow for
drastically reduced transient times because of the additional thrust (F=ma) [5].
Current Status
Today, designs are being reviewed and compared. The most promising
option is to utilize the NERVA program’s engine with modest design modifications.
The costs to restart the program include:
|
Cost in millions of dollars |
Design and construction |
1,218 |
Technology |
377 |
Capital |
460 |
Operating |
210 |
Total |
2,265 |
The total cost, including a full power test station, to rebuild a
NERVA engine run from $3 - $5 billion (FY 1985) dollars [5].
Nuclear Thermal Propulsion vs. Chemical Propulsion
The final question is which type of propulsion to use. The advantages
nuclear propulsion offers include:
- Shorter mission time
The time for a manned mission to Mars using nuclear
thermal propulsion is 200 days. This is one third the 600 days required for
chemical
propulsion. This reduced time is due to the
drastically increased thrust given by the nuclear thermal propulsion.
- Lower operating costs
Before a Mars mission is undertaken, all of the mass
for the payload, engine and most notably, fuel, must be placed into Earth orbit.
Using all
chemical propellant requires 46 additional launches
(compared to nuclear thermal propulsion) to get all of the fuel into Earth orbit
where it can be
utilized for a Mars mission. With a cost of $.15
billion per launch, $6.8 billion is saved using nuclear.
Despite these advantages, some disadvantages must be overcome
before an engine is even considered:
- Radiation dose to crew.
A nuclear engine will give off tremendous amounts of
radiation. Before use of these engines is even considered, an effective
shielding mechanism
must be developed.
- Development must be completed
Despite being near operational status in the 1970s,
no nuclear engines have ever been used. Therefore, before an engine can be used
on a manned
Mars mission, the engine must complete development.
The good news for nuclear thermal propulsion is that the radiation
problem has already been solved, as described earlier. A combination of shields
can protect the crew, exposing them to only a 10 REM dose. By comparison, US
civilians are to never exceed a 150 REM dose and military personnel are not to
exceed 500 REM.
Despite the disadvantages of nuclear propulsion, it is obvious that
this technology would be needed and preferred over conventional chemical
propulsion in a manned mission to Mars. The lower weight, lower overall cost,
lower fuel consumption, and greatly higher thrust production help make nuclear
propulsion a unanimous choice for interplanetary travel.
Conclusions
Nuclear thermal propulsion is the best near–term method for powering a
Mars mission. The engine offers lower costs and quicker travel times. In the
1970s, a nuclear thermal engine had been thoroughly tested, and restarting this
program will cost $3 - $5 billion. Finally, the complex shielding, necessary for
any nuclear device, has already been designed and additional concepts are on the
drawing board.
By contrast, chemical propulsion is bulky, heavy, expensive and slow.
Despite using it for several decades, continued use could potentially raise
costs to unaffordable levels. While many different materials can be used as
propellants, the more effective materials are usually quite expensive, and the
amount of propellant needed greatly increases this cost. This large amount of
propellant needed also adds a very significant amount of weight to the rocket,
decreasing its potential payload. The current state of chemical propulsion is
near a maximum, as the main engine on the Space Shuttle is near the upper limit
of the theoretically best chemical engine.
References
Chemical Propulsion
[1] C. D. Brown, Spacecraft Propulsion, 2nd ed. , Washington, DC:
American Institute of Aeronautics and Astronautics, 1996.
[2] M.F. McKay, D. S. McKay, M. B. Duke, Space Resources: Energy, Power,
and Transport, 2nd ed. , Washington, DC: National Aeronautics and Space
Administration Scientific and Technical Information Program, 1992.
[3] The Space Shuttle Clickable Map, SSA-National Web Team, [Website], 1998,
[cited November 22, 1999], Available
http://seds.lpl.arizona.edu/ssa/docs/Space.Shuttle/index.shtml
[4] Rocket, Encarta 96, Microsoft, 1996, CD-ROM.
Nuclear Propulsion
[5] Howe, Dr. Stephen D., Assessment of the Advantages and Feasibility of
a Nuclear Rocket for a Manned Mars Mission, Los Alamos: Los Alamos National
Laboratory, 1985.
[6] Nuclear Thermal Propulsion, INSPI, [Website], Dec. 30, 1998, [cited
November 22, 1999], Available
http://www.inspi.ufl.edu/research/ntp.html
[7] Space Exploration Initiative - Nuclear Thermal Propulsion, J. Pike, [Website],
[cited October 22, 1999], Available
http://www.fas.org/nuke/space/c07sei_1.htm
Back
Hiçbir
yazı/ resim izinsiz olarak kullanılamaz!! Telif hakları uyarınca
bu bir suçtur..! Tüm hakları Çetin BAL' a aittir. Kaynak gösterilmek şartıyla siteden
alıntı yapılabilir.
The Time Machine Project © 2005 Cetin BAL - GSM:+90 05366063183 -Turkiye/Denizli
Ana Sayfa /
index /Roket bilimi /
E-Mail /CetinBAL/Quantum Teleportation-2
Time Travel Technology /Ziyaretçi
Defteri /UFO Technology/Duyuru
Kuantum Teleportation /Kuantum Fizigi
/Uçaklar(Aeroplane)
New World Order(Macro Philosophy)/Astronomy
|
|